General Information on GRP Pipes, Raw Material and Production Process
Read about:
GLASS REINFORCED PIPES
PRODUCTION PROCESS
PRODUCT RANGE
FITTINGS
MANHOLE LINERS |
GLASS REINFORCED PIPES
Definition: Glass Reinforced Pipes (GRP) Pipes are made from glass fiber reinforcements that are embedded in cured thermosetting resin. GRP Pipes may
contain aggregate granular.
The selection of proper material as well as material composition depends on the pipe required properties and as well as designed performance characteristics.
GRP pipes were introduced since 1948. Since then GRP invaded the market due to its corrosion resistance capabilities and were selected as alternative to steel and stainless
steel pipes.
GRP pipe line expanded to include applications of high pressure, as well as big range of diameters reaching up to 4000 mm.
GRP pipes combine the benefits of durability, strength, and corrosion resistance; moreover, they offer great design flexibility with the possibility to customize the pipe
design in a wide range of properties, the same is applicable to providing a wide range
of different fittings profile and shape. |
|
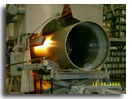 |
|
|
Materials: |
|
GRP pipes consist of:
Glass Fiber Reinforcement: the mechanical strength of GRP pipes depends on the amount, type and arrangement of glass reinforcement. |
The common glass types used in the GRP pipes are:
Designation |
General Application |
E |
Good electrical resistance |
ECR or Advantex |
Good Acid resistance |
C |
Good Chemical resistance |
|
|
|
Fiberglass Reinforcements are available in different forms:
Continuous Roving, consisting of bundled, untwisted, strand. It provides excellent mechanical properties.
Reinforcing mat, consisting of chopped strands held together with binder. It is used to provide multidirectional reinforcement in pipes as well as fittings
Surface Veil, are of light weight that allow high resin content layers, that helps in improving the environmental resistance of pipes and fittings, in addition to smooth surface.
Resins: only thermosetting resins are used in the production of GRP pipes. Thermoset resin are polymeric resin cured by heat or/and chemical additives. |
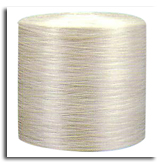  |
Resins could be of two types:
- Polyester, such as Isophthalic, that is commonly used to manufacture large diameter pipes used for conveying water and sewage. Vinyl ester, is another polyester, but have increased corrosion resistance and is commonly used to convey aggressive fluids such as acids.
- Epoxy resins are commonly used to manufacture small diameter pipes to convey water, hydrocarbons, diluted acids, …
- Additional components might be used in the GRP pipes such as: Silica Sand, Organic Peroxides catalyst, hardeners and accelerators … |
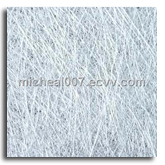 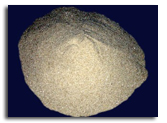 |
|
|
|
 |
|
|
PRODUCTION PROCESS |
|
|
|
GRP pipes are produced by Dubai Pipes Factory by either the Continuous Filament Winding or by the Reciprocal Helical Winding process. Both are considered as filament
winding machines, which is the process of impregnating a number of glass reinforcement with resin, then applying the wet fibers onto a mandrel in a prescribed patter. |
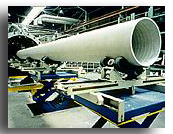 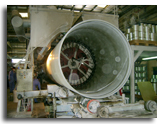 |
|
|
Continuous Filament Winder: A continuous winder is composed of a continuous steel band supported by beams which form a cylindrically shaped mandrel. The beams rotate, friction pulls the band around and roller bearings allow the band to move longitudinally so that the entire mandrel continuously moves in a spiral path toward the end of the machine. |
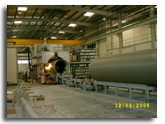 |
|
|
As the mandrel moves, raw materials, like glass fibers, resin, aggregate (if needed) and surface veil are metered on in precise amounts under the direction of a programmable logic controller (PLC) and computer (PC). After pipe is cured a synchronized saw unit cuts the pipe to the proper length.
Continuous winding process is considered as the most efficient, since once pipe production starts, as described above, the production process continues and would only stop at the completion of full order. This process is considered continuous since it does not hold and resume at the completion of each pipe or pipe layer. |
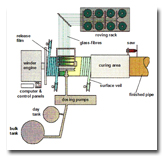 |
|
|
Reciprocal Helical Winding: is the process where the glass rovings, continuous roving specifically, passes though a resin bath for resin impregnation. Resin bath and glass directing comb are placed on a carriage that is driven back and forth at a very well controlled linear speed. Fiberglass, pre-impregnated with resin, are winded on steel mandrel that is rotating at determined RPM. The synchronization of carriage linear speed as well as the mandrel RPM determines the angle of which roving are winded on the mandrel, which is considered to be the glass winding angle, that is redetermined depending on the pipe requested property. For this reason, both the mandrel RMP and carriage speed are very well controlled by a computer program. |
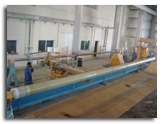 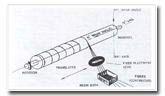 |
|
|
In this process, winding progress is in stages, were multiple linear movement of carriage would produce one layer of pipe thickness, and pipe thickness is composed of multiple layers, depending on required total thickness. |
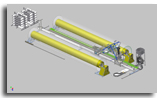 |
|
|
For all processes, GRP pipes are made from many layers, the main layers are:
- Inner liner, which is rich with resin and is to provide chemical resistance to the pipe and well as well as smooth inner surface. Inner liner thickness that could reach up to 2.5 mm
- Structure layer, which is forming the majority of pipe thickness. Pipe mechanical strength is mainly achieved by the structural layer.
- Outer liner, which is as well rich with resin and is to give environmental protection to the pipe thickness. |
 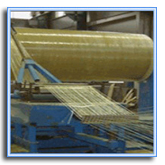 |
|
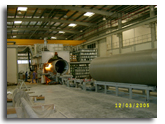 |
|
 |
PRODUCT RANGE |
|
Dubai Pipes Factory Co. Produces pipes with a diameter range up to 2400 mm.
GRP pipe standard pressure ratings includes gravity, 6, 9, 10, 12, 16, 20, 25 and 32 bar.
GRP pipe standard Specific Tangential Initial Stiffness includes: 2500, 5000 and 10000 N/m2.
The manufactured standard pipe length is up to 12 m.
Any other customized product for any application could also be designed and manufactured. |
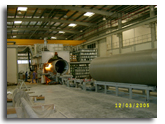 |
|
|
|
 |
|
|
MANHOLE LINERS |
|
Manhole liners are made in Dubai Pipes Factory in whatever shape required. Where a thin pipe produced at the winder is used to form the manhole shaft; whereas cover slab with the required opening is sprayed on a pre-formed mold. Sprayed cover slab are also produced using glass fiber and resin identical to the ones used for pipe production. Cover slab could be jointed to the shaft either in the plant or they could be jointed on site by either lamination or by the use of bell month, which is the coupling type of joint.
|
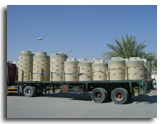 |
|
 |
|
|
|